Transforming robots from repetitive machines into cognitive collaborators
Today’s industrial robots are transforming radically, metamorphizing from rote machines into cognitive collaborators. They’ve become an integral link in a dynamic continuum that encompasses humans, other machines, and the digital environments in which they operate: In a factory in Turin, Italy, a three-ton robotic arm senses through human-inspired “skin,” deciding whether to reduce speed or stop operations altogether. Its 3-D camera eyes materials that need to be retrieved, and it relies on its sense of touch to grip them properly. An advanced laser scanner monitors the workspace while the arm is in operation and alerts the robot to be careful when humans are nearby.1
A nexus of sensors, including computer vision, sensing ‘skin,’ positional feedback, and work cell monitoring, will insure safe cobotic interaction.
The relationship between humans and robots will soon deepen, thanks to affective computing. “Today we have rudimentary capabilities in software and hardware to perform sensory responses within given environments,” says Wind River® CPO Cyra Richardson. “As robots are taught how to respond to human emotions, and as engineers abstract lessons from human evolution about how people see, move, balance, hear, and feel, we will be able to better understand how cognition works. The sensing abilities of robots will grow and automation ecosystems will expand.”
The scope of environments that can be monitored will also grow as tiny sensors, aka smart dust, collect and analyze information from vast terrains. Implanted in humans, smart dust could help control pain or cure deadly diseases. Sprinkled around a city, it could monitor vibrations, temperatures, and magnetic or electrical fields. Therein lies the foundation of a smart city.
These advancements mean that automation ecosystems currently operating in controlled environments, such as a factory floor or a space satellite, will be adaptable to more chaotic and unpredictable environments — think autonomous vehicles driving on busy city streets, or humanoid robots helping the disabled navigate crowded sidewalks.
The cognitive capabilities of robots are already becoming indispensable as the COVID-19 pandemic reveals an urgent need to create more resilient supply chains and protect human workers. Work-related restrictions are driving the creation of an automated continuum involving humans and robots in industrial manufacturing. In warehouses, collaborative robots — cobots — work alongside humans to accelerate tasks such as reading orders, picking and packing products, and shipping them. At a DHL facility in Wilkes-Barre, Pennsylvania,2 workers averaged from 70 to 80 picks per hour prior to the arrival of a fleet of cobots. Now cobot-assisted picks range from 150 to 180 per hour.
Advanced robotics are expected to add up to $4.5 trillion to the global economy by 2025, according to McKinsey.3 By 2026, cobots designed to share workspaces with humans will see an estimated compounded annual growth rate of 45%, according to ResearchMarkets. And the International Federation of Robotics recently reported that service robot sales were up 32% worldwide, largely driven by COVID-19.4
One subset experiencing particularly high growth is logistics robots — up 110% year on year. Such autonomous mobile robots were initially used in warehouses, but with the ongoing digitalization of production, they’re quickly becoming part of today’s smart factories. Another category surging in the COVID-19 era is robotic surgery systems. By 2022, medical robot sales have the potential to more than double.
1 "Robots Partnering with Humans," Robotics Tomorrow, December 2020
2 "DHL – High Performance Warehouse and Retailer Picking," Locus Robotics, September 2020
3 "Disruptive Technologies," McKinsey Global Institute, May 2013
4 "Service Robots Record: Sales Worldwide up 32%," International Federation of Robotics, October 2020
5 "Collaborative Robots Improve Quality," Quality Magazine, April 2020
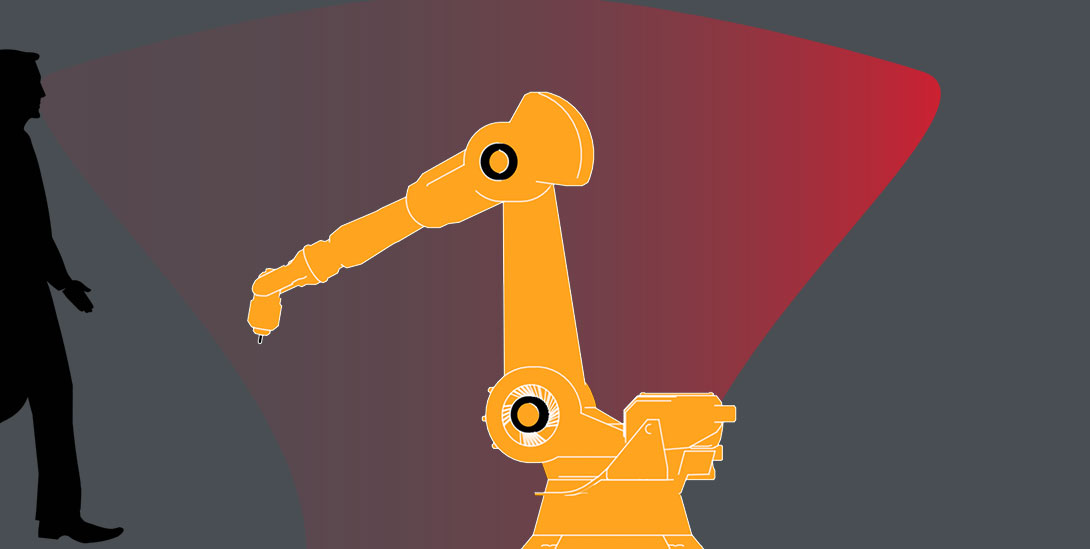
Large six-axis industrial robots are used in places like car factories to do repetitive, laborious tasks. They are usually bolted in place at the base, but the arm of the robot still has a wide range of movement in all directions.
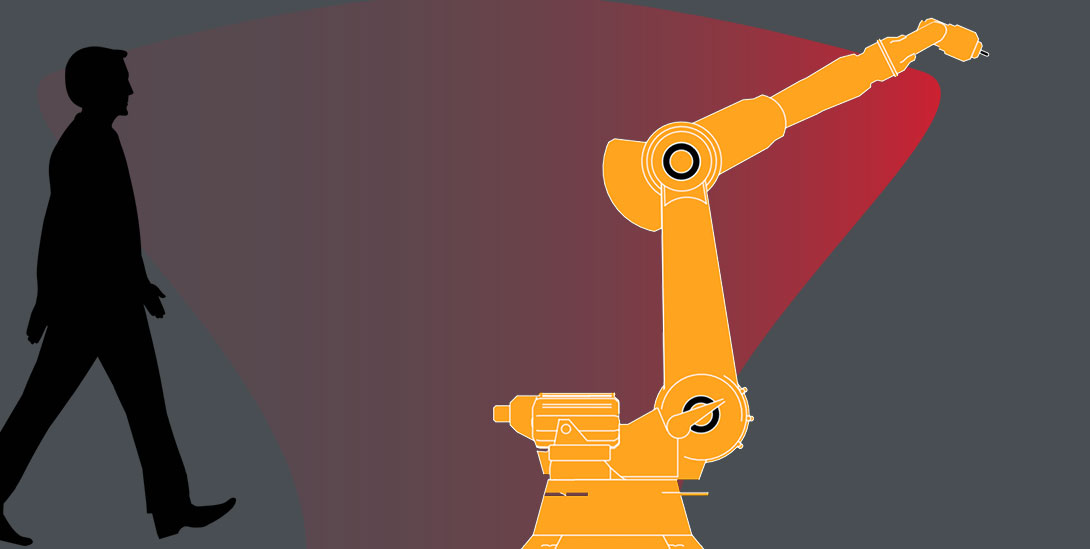
Each robot has a sensory perimeter or work area that extends in all directions to the limits the robot can reach.
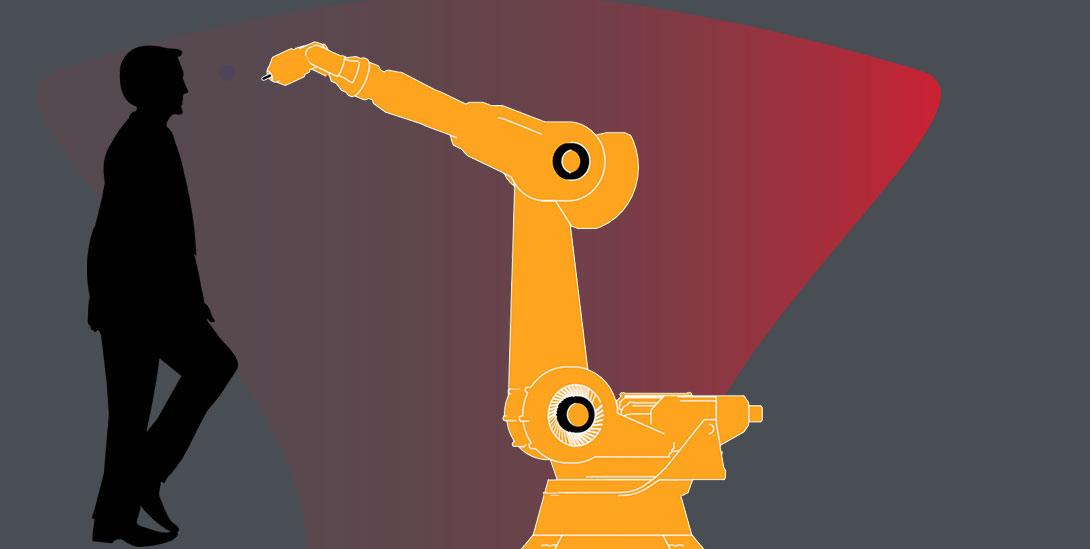
These robots are increasingly working in proximity with human counterparts, rather than being isolated from people.
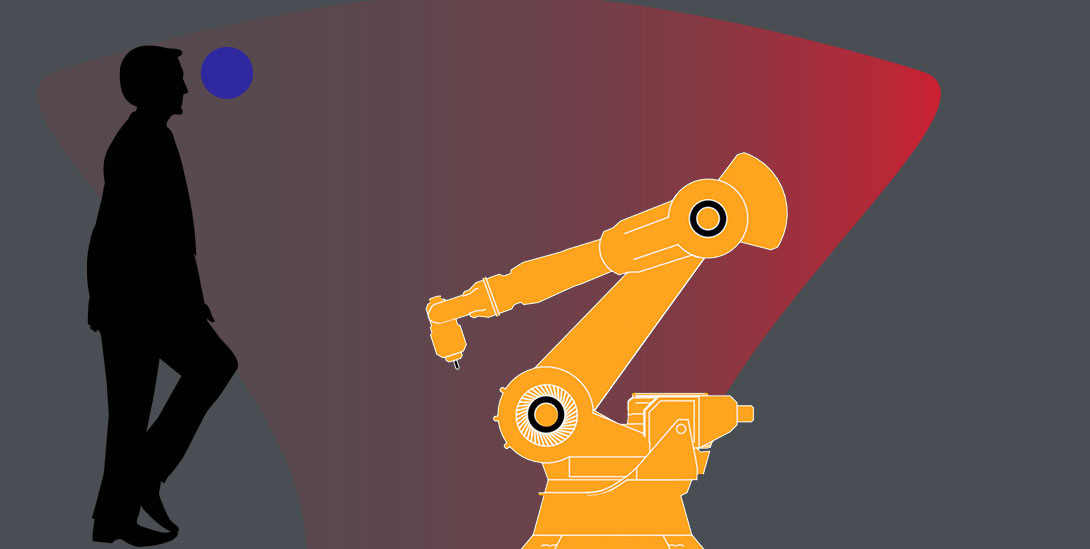
To protect human workers, the robot collapses to a safe position when a human enters the robot’s sensory perimeter.
Chief Product Officer
Wind River